Key WMS Reports and Dashboards for a Warehouse or Distribution Center
Your company has taken an important step towards the future by investing in warehouse management software. One of the major drivers behind this may have included increasing the operational efficiency of both labor and physical space by harnessing the real-time visibility of goods and space in the warehouse. This is critical to help design a sound supply chain strategy at an enterprise level. The visibility that a Tier-I WMS like Blue Yonder offers must also be leveraged by Warehouse Managers and Supervisors to stay ahead of any potential issues and bottlenecks, which left unattended could result in a hit on operational efficiency and eventually affecting SLAs. In this post we present the critical WMS reports and dashboards for a first-class warehouse manager that’s on top of their game, and as a bonus for those of you with Blue Yonder WMS we’ll show you where to find each report/dashboard.
1. Door Activity
Your one stop-shop to assess the status and utilization of your dock doors and yard. This is a pretty neat dashboard (screenshot below) that you can use to monitor the receiving and shipping progress as it relates to the transport equipment checked in to a dock door, or you can view the equipment parked in a yard location. This dashboard also gives you the ability to generate yard or door audits, and reconcile any equipment mismatches with the corresponding doors. Should you need to move around loads in order to maybe accommodate ‘hot’ loads, you can instruct your yard personnel to do so with this dashboard. The dashboard also utilizes several intuitive tags such as “Live”, “Safety”, “Over” etc. that gives you the most important information at a glance.
Where to find in BY WMS: Yard -> Door Activity Page
2. Shipping Dashboard
You can use the shipping dashboard to view information on the progress or lack thereof planning, picking, and shipping activities for a specific date and time. This dashboard gives you a glance into critical information relating to shipping issues such as short loads, un-shippable or problem inventory (maybe due to holds or damage), and issues relating to staging such as loads held up due to lack of staging lanes. It is crucial that your shipping supervisor/ or manager stays on top of these issues, and acts immediately to resolve them as they have the most impact on fulfillment within SLAs. This dashboard also gives you the ability to look at fulfillment progress by inventory levels, loads, and shipments with a neat bar graph that can be adjusted for date and time. Other information accessible from the door activity is also conveniently grouped into this dashboard such as late appointments, live loads, dispatch ready loads etc.
Where to find in BY WMS: Shipping -> Dashboard
3. Location Error Report
Locations that are set ‘out-of-service’. These locations will not be considered by directed tasking for storage, replenishment, and fulfillment activities. A location may be set out of service for a number of reasons including mismatched physical and systemic inventory, a broken pallet currently in location, the rack has structural damage from a forklift bump etc. Leaving these issues unattended for an extended period of time will result in decreased space utilization and losing money, especially if it’s a forward pick-face. You will also likely want to get any structural damage addressed before it turns into a catastrophic failure.
To find out what locations are currently errored out, utilize the Blue Yonder WMS Inventory Dashboard. Try to resolve the errors by generating a count for mismatched locations, moving damaged inventory out, or physically inspecting the location for damage.
4. Receiving O/S/D Report
Overages, Shortages, and Damages during receiving. Stay informed of variances in actual vs expected receipts as this may affect fulfillment and in a larger sense, demand planning. If damage-in-transit is above acceptable thresholds then it could be time to renegotiate terms with the supplier. This report is a good tool to assess your suppliers and their compliance to your standards of fulfillment, and packing.
Where to find in BY WMS: System Administrator -> Operational Reports. You can run this report by inbound shipment, supplier, or a date range.
5. Late Orders
Orders that have been collecting dust. The bottom-line for any warehouse or Distribution Center is, well, order fulfillment. You are going to want to stay on top of potential issues with orders that could delay fulfillment, incurring costly penalties for failing to meet SLAs. Maybe a handful of orders have gone short, or maybe there is a bottleneck in shipping preventing staging and loading few orders.
Where to find in BY WMS: System Administrator -> Operational Reports. Open the ‘Unprocessed Demand’ report, and order by ship date.
6. Count Variance Reports
Locations with mismatched physical and systemic inventory. This report gives you an opportunity to assess the cause of the variance and refine your warehouse processes accordingly. Maybe there is a problem process that is common, or maybe there is a poorly placed case label that the operators are scanning on to the location instead of the pallet label. Left unattended, you may think you have inventory that you don’t actually have.
Where to find in BY WMS: System Administrator -> Operational Reports. You can get reporting of variances by locations as well as items.
There very well could be other reports/dashboards that are more critical for your specific operation, but the above recommendations should be a good starting point for most warehouses. Let us know what warehousing reports you rely on! Drop us a line and we’ll compare notes.
This post was written by:
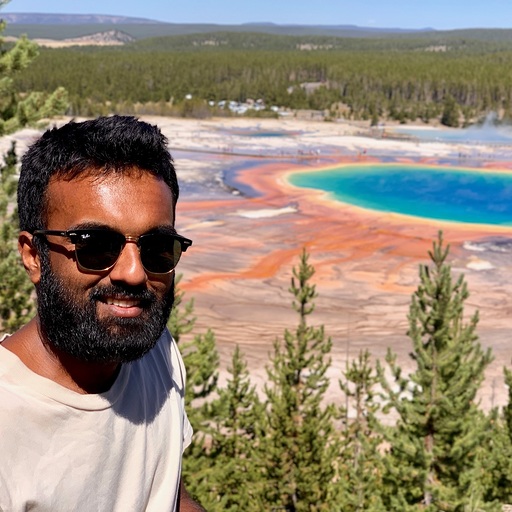
Balaji Raman Senior Solutions Engineer Balaji has several years of experience solving clients’ supply chain execution problems, specializing in Warehouse Management Systems. He prides himself in building meaningful relationships with stakeholders and being a trusted advisor to his clients. In his free time Balaji enjoys travelling, hiking, and exploring new cities by running around them. Drop him a line at: balaji.raman[at]tryonsolutions[dot]com.
Recommended Content
Successfully Upgrading to Blue Yonder SaaS Despite Mid-Project Scope Expansion
This case study explores how our team successfully managed and completed a Blue Yonder SaaS upgrade despite significant mid-project scope expansion. Discover the challenges faced, strategic adjustments made, and best practices applied to keep the project on track,...
6 Levers for Smarter WMS Support
Whether you're juggling school drop-offs, remembering a birthday party, or trying to reply to that one group text before dinner hits the table, modern life pulls us in a hundred directions at once. That constant pressure to keep up, stay flexible, and deliver—no...
Executive Checklist – Is Your WMS Supporting Business Strategy
This executive checklist from Tryon Solutions helps leadership teams assess whether their Warehouse Management System is truly aligned with business strategy. Explore key areas like scalability, customer experience, operational efficiency, and innovation to identify...
From Cost to Value-An Executive Guide to WMS ROI
Unlock the full ROI of your WMS with this executive guide from Tryon Solutions. Discover how services like testing, integration, and continuous optimization drive long-term value far beyond go-live.
WMS Lift-and-Shift the Top 10 Reasons to Move from On-Prem to SaaS
Over the last couple of years there has been a major push on all enterprise systems to move to the cloud. This includes ERP, CRM, HRIS, PLM, SCM, BI, MES, etc. The acronyms could go on forever. Each organization has their reasons for the move, but most fit into three...