Use a WMS to Help Calculate Safety Stock
This past year we’ve been seeing warehouses carrying more safety stock to help offset supply chain disruptions. Safety stock is an extra “buffer” of inventory in the event demand increases unexpectedly and/or supply chain issues (like supplier delays, port problems, etc..) prevents you from replenishing one ore more items of inventory. There is a need for this cushion, as “stockouts” result in nearly a trillion dollars in lost sales worldwide every year. Service levels must remain high in our current environment of cutthroat competition, as any real drop-off can negatively affect your company’s reputation. BUT…and we all know there is always a “but”, too much safety stock increases carrying costs and certain types of products (high tech, perishables, etc…) could depreciate in value while gathering dust in storage. Please note that “Safety Stock” is different from “Working Stock”, which is basically the amount of inventory available to meet the expected demand during a specific timeframe.
A warehouse management system helps via:
- A WMS improves the things that you can control, to make it easier to focus on what you can’t
- The historical data behind inventory items can help forecast what is needed for the future
- The overall optimization and accurate reporting of what’s in the warehouse makes it easier to set aside adequate space for safety stock
- A WMS can help fill the variables in your safety stock calculation
Safety Stock = (max number sold per day X maximum lead time in days) – (average number sold per day X average lead time in days)
Let’s try this formula using an actual, real-world situation with a totally realistic product…So your warehouse backs up a Spoiled Egg Flavored Lip Balm outlet located nearby.
Your shop had a great day a few weeks ago thanks to a promotion and sold 137 tubes of balm, and you know that the longest time it would take to get a fresh shipment is 12 days. Now on your average day the store sells around 90 tubes, and the average lead time to get more is 7 days.
Let’s plug the numbers into our formula:
(137 tubes X 12 days) – (90 tubes X 7 days) = 1,014
Your warehouse should keep 1,014 tubes of Spoiled Egg Lip Balm as safety stock
While this formula can help determine an adequate safety stock level, keep in mind that it doesn’t take into account either supplier or logistical reliability. Also, seasonal shifts and – really supply and demand overall – is extremely dynamic these days. We also know that fickle customers could lose their taste for spoiled egg flavoring, and so you will need to keep the above formula up-to-date to maintain proper levels of safety stock.
How do you calculate safety stock? Drop us a line and we’ll compare notes.
This post was written by:
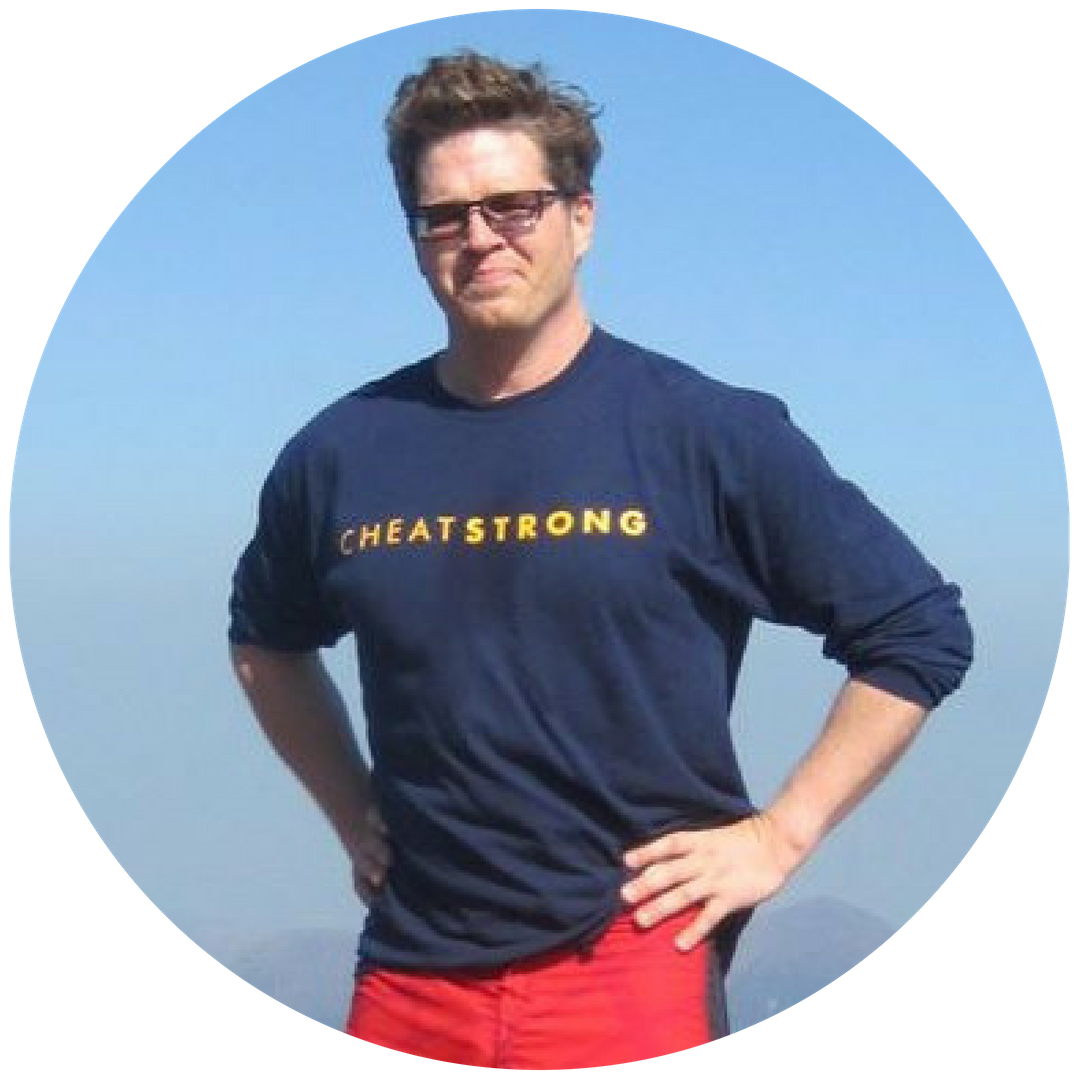
Recommended Content
How to Prep and Undertake a Supply Chain Execution Go Live as a Client
You’ve chosen a supply chain execution system (WMS, WLM, etc…) along with a vendor to handle the implementation, and all parties have agreed upon on a timeline. So…What’s next? We can sit around patting each other on the back for finally bringing our operation...
Similarities between Manufacturing Supply Chain and the Human Body
What? Come on now… How can an efficient manufacturing supply chain be similar to a healthy human body? They got nothing to do with each other? One is a living organism…and one is…well…an industrial process. Actually, the count is endless. A well oiled industrial...
6 Tips to Properly Maintain Your Warehouse Management System
Your operation has successfully implemented a warehouse management system. Congratulations, as not all WMS implementations are successful – or so we hear, at Tryon Solutions we don’t have firsthand experience with that. Your next step post-implementation is ensuring...
5 Supply Chain Systems Enhancements for Consumer Goods
Line up! The battle for the top systems enhancements for consumer packaged goods (CPG) companies starts now. Every single supply chain professional has their own list of tools needed and processes required. Every organization has their inventory issues with changes to...
4 Compelling Reasons to Outsource Supply Chain Execution Services
Why would one outsource when it’s technically possible to handle everything in-house? I’m a fan of a nice haircut, and I’m willing to pay a little more to get it. Before coming to this conclusion, I tried a well-known super-cheap option out there (rhymes with...