TRYON BLOG
Warehouse Management Systems: Origins and The Future

Warehouse management systems have come a long way from the humble origins of a simple inventory list in green text to a complete, sophisticated system that orchestrates the optimized movement, storage, and retrieval of inventory with detailed reporting at every stop. The journey of WMS technology is a testament to ingenuity, but also the relentless march of progress in the supply chain demanded by the needs of commerce. In this article let’s briefly navel gaze on where WMSes came from, after that we’ll look at where we are now, and finally let’s speculate – both conservatively and wildly – where things are headed.
Early Warehouse Management Systems:
One could make the argument that the first WMS was perhaps a Stone Age club wholesaler that organized his wares in a large cave (warehouse) by size and popularity (slotting) and after a few sales Grog would go and retrieve them (wave pick) in an organized manner (route optimization), and then of course trained sabretooths and mammoths (for XXL two-handed options) would deliver the clubs. Good luck designing a TMS for a fleet of sabretooth tigers and wooly mammoths. While that’s a fun thought, we’ll start with the first electronic solutions.
Early WMS systems (McHugh Freeman and Demag among others) emerged in the mid-1970s into the early 1980s, and automated very basic warehouse operations. Many were mainframe based, and focused on inventory tracking with a crude level of management functionality and reporting. There were no helpful GUIs and nothing was automated. The WMS user would enter commands into a prompt which would then return inventory information in green text. While simple and light on features, these barebones systems were workhorses that laid the foundation for what we have today.
Evolution of WMSes to Present:
Warehouse management systems have evolved to meet the growing demands of the supply chain, and cutting-edge technology is quickly harnessed as it becomes more readily available. User directed put-away and order picking have given way to faster, more accurate system directed options. Interfaces drastically improved from the blinking cursor awaiting input to an actual user-friendly GUI. Integrations went from being made-to-order from scratch to having universal standards. Hardware, especially label printers and scanners, have seen drastic improvements including barcodes going from 1D to 2D to RFID as well the scanner input screens going from overly basic, to an actual GUI, and finally on to being a legitimate mobile application that runs on your phone.
The WMS vendors themselves are continually trying to reduce maintenance, and one key way is via less customization and more configuration. Filling a warehouse with personnel was straightforward in the old days, but over time (and toss in an unpredictable labor market) it’s a more science-based calculation that has resulted in the rise of labor management systems and robotics.
Where we are Now:
While a warehouse management system may have been a nice-to-have in the 1980s and even into the 1990s, in modern times medium-to-large warehouses and distribution centers don’t have the luxury of choice in order to compete. The WMS is now a central, integral component of supply chain management. Every last micro-ounce of efficiency and cost must be squeezed, as competition is brutal and we live in a world where consumers expect their products within a day. Some customers even insist that their shippers adopt a WMS to adhere to their compliance requirements.
The chance for human error has been greatly reduced from the early WMS days where inventory was simply tracked, as today a WMS “guides” inventory through receiving, put-away, inventory management, picking, and shipping while optimizing these processes and advising on inventory replenishment. A modern WMS can instantly check to see if a product is available for an order, whereas even in recent memory this would be handled by a human, who would take too long, and all too frequently mess things up.
A modern-day WMS can work in tandem with labor management and transportation management systems, and thus increase the efficiency of logistical movements. There is also no shortage of integration possibilities with automation systems and robotics solutions, and this arena is the future of warehouse management.
Conservative Estimate on the Future of WMSes:
The WMS future is bright even if we reign in our imagination. We’ll continue to see easy-to-use interfaces, as the uncertain labor market will demand it, and these front-ends won’t be on-premise as the SaaS push rolls-on with customers increasingly choosing the security and scalability of the Cloud. We are also seeing more “pay for what you need” customizable WMSes coming with out-of-the box integrations hitching up to the variety of emerging warehouse technology being released seemingly daily. AI and machine learning technology will march onwards from order picking to everywhere else in the warehouse, and we’ll start to see drones counting in large warehouses with tall racks. Robotics and automation are just getting started, currently used mainly for putaway and picking, but will branch out everywhere in-and-out of the four walls of the warehouse.
Wild Speculation on the Future of WMSes:
Let’s speculate more wildly on what’s coming further into the future: A consumer expecting same-hour delivery places an order that instantly becomes a pick in the WMS. The Robo-Picker 5000 races to requisite pickfaces, pulls all of items for the order, and hurries to the outbound dock. Small items are offloaded from the Robo-Picker right onto the drone, and any larger products are placed on an autonomous delivery vehicle. The drone delivery reaches the eager customer within the hour, and any larger purchases arriving via autonomous truck will take within 24 hours.
In this futuristic example, the artificial intelligence powered WMS is the brain behind a dark warehouse full of robots. Every logistical movement is streamlined to the fullest, and there is no need for supplemental processes like cycle counting or user training since AI controlled robots handle everything. There could be large and/or intricate machinery that still requires humans at the reigns, and in those cases a driver/pilot will remotely helm the equipment.
AI will eventually not only oversee warehouse operations, but it will also analyze large amounts of consumer data and forecast the necessary inventory replenishments and related warehouse configuration/layout to handle the upcoming orders. It can take things into account like customer trends and even the weather; widespread hurricane devastation could likely result in a rush on building materials. What else is the AI doing? Maybe an idle drone or two flies over the competition’s warehouse to see what’s going on…
Of course, the advantage of having the most state-of-the art “warehouse of the future” is totally negated if its isn’t managed well. If your team could use some operational consulting then feel free to drop us a line, as this is our specialty.
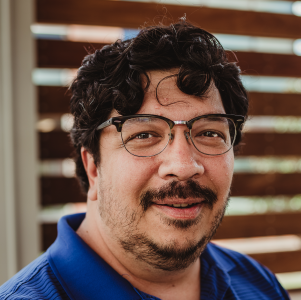
Co-Written By Brian Perrault
Brian is an experienced Enterprise Consultant specializing in keeping Warehouse Management Systems regularly upgraded, secure, and thoroughly tested for optimal performance. For further information, please email sales@tryonsolutions.com.
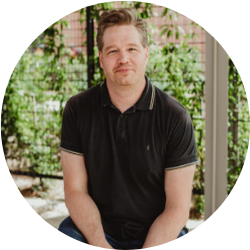
Co-Written By James Prior
With over two decades in software pre-sales and implementation since 2000, James specialized in working with pre-sales teams and contributed to blog posts. For further information, please email sales@tryonsolutions.com.
More From This Category
6 Levers for Smarter WMS Support
Whether you're juggling school drop-offs, remembering a birthday party, or trying to reply to...
WMS Lift-and-Shift the Top 10 Reasons to Move from On-Prem to SaaS
Over the last couple of years there has been a major push on all enterprise systems to move to...
5 Signs Your Software May Not Be FSMA Rule 204-Compliant
Is your current software keeping up with the new requirements of FSMA Rule 204? If you're not...