We Saw Robot Picking in Action...
An efficient operation is no longer a “nice to have” in this era of labor shortages and ruthless competition. We recently toured the warehouse of a large electronics company located in the Southern United States that saved 35,000 US dollars a month while increasing employee morale by automating the most intensive part of their picking process with robots. The warehouse personnel saw the robots/cobots coming, and instead of “best worst-case” replacing them and “worst-worst case” something like the Terminator, the bots helped them do their jobs!
This operation has a 350,000 square foot facility that ships 1.3 million units a year. They all-too-often had problems with slow cart picking, frequent errors that require re-picks, and bottlenecks with their dimensioning systems. The slowness was mainly due to personnel hauling inventory between picking and packing, and the lack of accuracy was due to these same tired workers performing manual verifications.
The head of IT recalled seeing Locus Robotics demonstrate picker cobots at a previous MODEX tradeshow – and the seed was planted. In January 2022 they leased 20 Locus cobots to pick for packing, and were told they can scale the number of bots depending on the season.
The picks and cartonization are all ironed out via Blue Yonder WMS “before the bot”. Here is a basic breakdown of their process post-implementation:
- The packer puts the shipping boxes on the bot, and the barcode that goes with the box tells it what item(s) to get
- The bot hustles over to the location of the inventory item(s), and during the trip it stays to the side of the main isles to avoid traveling the same paths as forklifts and other equipment
- The picker is wearing a Bluetooth identifier badge and so the bot knows exactly who is picking, and he or she puts items on the bot which are then photo verified on the bot’s screen (pictured below)
- Once the bot has picked all carton(s), then it returns to the packer station with the picked items for packout
If at any point the bot runs low on battery power, then it will break off for a top-off charge. The aforementioned Bluetooth identifier badge also helps ensure picker accountability and accuracy.
Despite introducing cutting edge technology, no major changes were made to their warehouse foot print, layouts or overall process flow. The robots adjusted to their operation, and NOT the other way around. We were told it took about 3 months to get fully rolling and that includes training, network installation, virtual mapping, WMS integration, and the robot/charger setup. One warehouse manager told us that the Locus folks are “Very responsive and good to work with.”
Picks Before Locus Bots: 110 units per hour
|
|
Picks After Locus Bots: 407 units per hour
|
![]() ![]() |
It took 11 months to pay everything back, and they are now enjoying a 35,000-dollar month savings. Along with the drastic increase in units picked per hour, there was also an 8 FTE reduction and a reduced error rate from 3.5 to 1.5 percent.
The biggest intangible benefit was reaped by their older workers who find themselves less worn out, as they no longer have to take arduous treks across the warehouse – and they better have a newfound “pep in their step” as the bots now the set the work pace at the picking and packing areas! Warehouse personnel are also able to cross-train and perform other tasks with their extra time.
Initially the workers were concerned about their steel colleagues joining them, but soon after implementation they were happy to find that the cobots made their job easier. The employees reported that they go home with more energy to play with their kids, go hiking, etc…and its safer in many ways to have cobots with cutting edge avoidance systems lugging inventory around versus people that have to rely on their eyeballs and human reflexes.
Fun facts:
- Isaac Asimov stated that “A robot may not injure a human being…”, and Locus Robotics strictly adhered to this principle as the bots will ALWAYS go around you. I tried to fool their sensors by doing a little shake-n-bake, but I never managed to trick them.
- The Locus Bots automatically learn the most efficient travel routes through a warehouse which dramatically improves worker efficiency and productivity over traditional cart picking, and the zone-based system allows for hands-free picking which virtually eliminates errors.
- The flexible design allows Locus Bots to be configured to meet a wide range of tote and multi-bin picking needs, and the lightweight design allows them to safely operate closely alongside workers and even in mezzanine configurations.
- The screen on the robot supports many languages with automatic translation depending on the Bluetooth badge worn by personnel.
- There is no maintenance, and most fixes are “plug and play” due to the modular construction of the bots. Via their own network, Locus Robotics keeps tabs from afar and will often alert the warehouse personnel of the occasional concern.
Tryon Solutions engineers handled the Blue Yonder WMS implementation and assisted with the Locus Robotics integration at our partner/friend’s facility in the Southern United States. Drop us a line if you have any questions on robotics integration and/or the Locus bots themselves, and be sure to check out this brief explainer video for more information.
This post was written by:
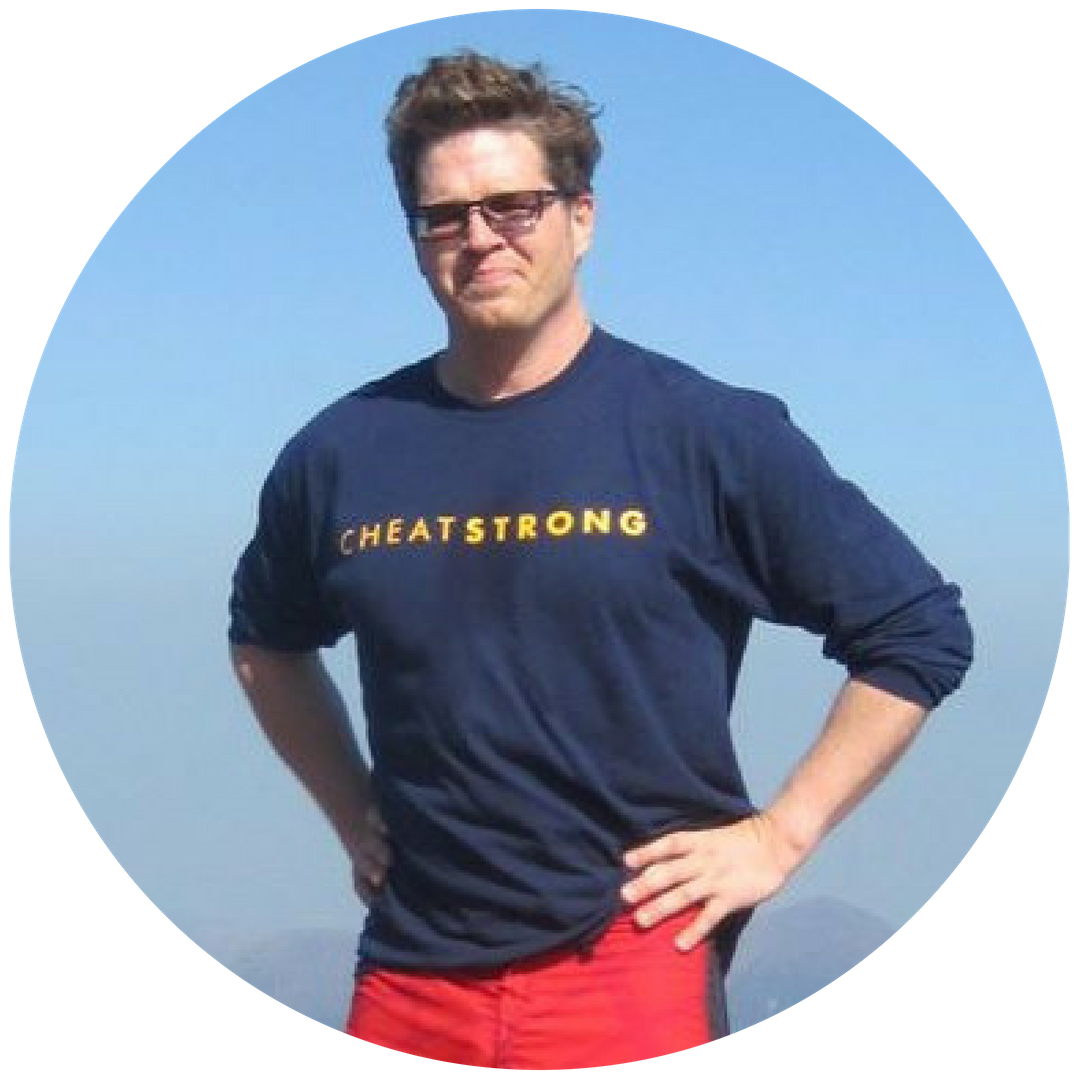
Recommended Content
How to Prep and Undertake a Supply Chain Execution Go Live as a Client
You’ve chosen a supply chain execution system (WMS, WLM, etc…) along with a vendor to handle the implementation, and all parties have agreed upon on a timeline. So…What’s next? We can sit around patting each other on the back for finally bringing our operation...
Similarities between Manufacturing Supply Chain and the Human Body
What? Come on now… How can an efficient manufacturing supply chain be similar to a healthy human body? They got nothing to do with each other? One is a living organism…and one is…well…an industrial process. Actually, the count is endless. A well oiled industrial...
6 Tips to Properly Maintain Your Warehouse Management System
Your operation has successfully implemented a warehouse management system. Congratulations, as not all WMS implementations are successful – or so we hear, at Tryon Solutions we don’t have firsthand experience with that. Your next step post-implementation is ensuring...
5 Supply Chain Systems Enhancements for Consumer Goods
Line up! The battle for the top systems enhancements for consumer packaged goods (CPG) companies starts now. Every single supply chain professional has their own list of tools needed and processes required. Every organization has their inventory issues with changes to...
4 Compelling Reasons to Outsource Supply Chain Execution Services
Why would one outsource when it’s technically possible to handle everything in-house? I’m a fan of a nice haircut, and I’m willing to pay a little more to get it. Before coming to this conclusion, I tried a well-known super-cheap option out there (rhymes with...