Top 7 Proactive Measures to Reduce WMS Support Headaches
(Pictured: Warehouse manager experiencing a WMS Support Headache)
During the WMS selection process your operation has hopefully chosen a top-tier warehouse management system like Blue Yonder, which can help reduce WMS support issues, especially as compared to your team using the beta version of Irving’s PocketWarehouse App. We all live in the real world and know that despite everyone’s best efforts there will inevitably be at least some support required whether due to faulty hardware, the odd bug, or the “new guy” that speed-skimmed the manual. These concerns can be time consuming and expensive, and so we polled our top WMS customer care guru at Tryon Solutions for his top 7 proactive measures to reduce WMS support headaches.
- Do not cut corners on hardware, whether getting servers up to the recommended specifications or properly covering the warehouse with Wi-Fi. Underpowering your WMS can at best result in a laggy system, and at worst bring on costly production outages. Error on the side of power for this expenditure, as hardware only becomes more stressed as the business grows.
- Your database admin should conduct routine maintenance, including things like archiving production database tables and rebuilding indexes. Neglecting the backbone of your WMS can cause a wide variety of issues including slow performance, database locks, and/or corrupted data.
- You should regularly test your supply chain systems to identify errors and validate business processes before production is impacted, as this can also aid in reducing support load. Rather than laborious manual testing, we can recommend a low-code test automation solution that makes creating and maintaining test cases as easy as possible.
- Douglas Adams famously penned, “A common mistake that people make when trying to design something completely foolproof is to underestimate the ingenuity of complete fools.” Users should be adequately trained and be armed with ample SOP documentation, and while Adams reminds us that “foolproof” is overly idealistic we can at least strive for “fool-resistant.” The more trained and informed a user is on their business process flows, the less likely they are to make a mistake and in-turn need to lean on support.
- Your operation should adopt a “stay current” update methodology to take advantage of the latest bug fixes/patches. It is a waste of everyone’s time (and in-turn money) to troubleshoot a problem that was ironed out in later versions. If you decide not to keep your system perpetually current, then at the very least you should be aware of the latest hotfixes and features available for your WMS as new versions are released. Also, don’t forget to check firmware and driver updates for any related hardware like scanners, label printers, etc…
- It is recommended to leave serious support concerns to the experts even if it must be outsourced, as opposed to involving an in-house C-team who “knows enough to be dangerous” that could further botch the situation. Production downtimes are much pricier in terms of business loss and potential reputation damage than the cost of outsourcing WMS support to professionals.
- Role restrictions are a must-have in the WMS world. Many unnecessary problems can be accidentally created by users screwing up a task they were not trained to perform. Imagine if a brand-new user in your operation’s small satellite warehouse in Montana randomly picks inventory in the giant distribution center in Atlanta that delivers to your company’s largest customers. Regardless of the size of your company, you should lock the WMS users down into their specific roles.
Let us know if you think we missed a tip or two, and we can certainly help if you are in the market to outsource your support for any product in the entire Blue Yonder suite; feel free to drop us a line.
Post co-authored by:
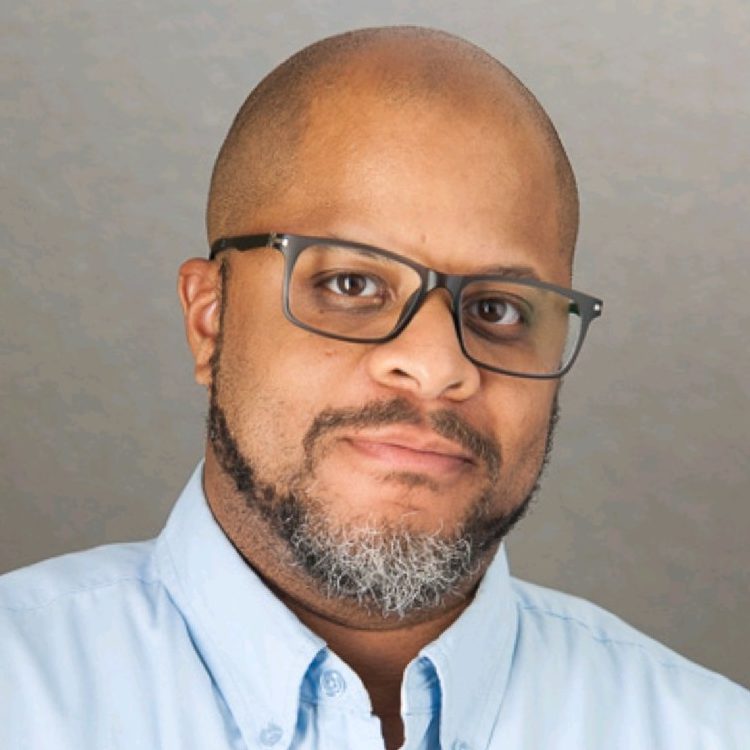
Brian Henry Customer Care Manager Brian has been working with supply chain applications, including the Red Praire/JDA/Blue Yonder suite, for 20+ years and has worn multiple hats throughout including Application Support, Development, Business Analyst, and Customer Care Manager. Drop him a line at: brian.henry[at]tryonsolutions[dot]com.
Post co-authored by:

Recommended Content
Successfully Upgrading to Blue Yonder SaaS Despite Mid-Project Scope Expansion
This case study explores how our team successfully managed and completed a Blue Yonder SaaS upgrade despite significant mid-project scope expansion. Discover the challenges faced, strategic adjustments made, and best practices applied to keep the project on track,...
6 Levers for Smarter WMS Support
Whether you're juggling school drop-offs, remembering a birthday party, or trying to reply to that one group text before dinner hits the table, modern life pulls us in a hundred directions at once. That constant pressure to keep up, stay flexible, and deliver—no...
Executive Checklist – Is Your WMS Supporting Business Strategy
This executive checklist from Tryon Solutions helps leadership teams assess whether their Warehouse Management System is truly aligned with business strategy. Explore key areas like scalability, customer experience, operational efficiency, and innovation to identify...
From Cost to Value-An Executive Guide to WMS ROI
Unlock the full ROI of your WMS with this executive guide from Tryon Solutions. Discover how services like testing, integration, and continuous optimization drive long-term value far beyond go-live.
WMS Lift-and-Shift the Top 10 Reasons to Move from On-Prem to SaaS
Over the last couple of years there has been a major push on all enterprise systems to move to the cloud. This includes ERP, CRM, HRIS, PLM, SCM, BI, MES, etc. The acronyms could go on forever. Each organization has their reasons for the move, but most fit into three...