TRYON BLOG
Top 5 Ways You Could Botch Your Next WMS Go Live

Are things running too smooth? Have you had it too easy in the supply chain world these days, and want to challenge yourself by botching a warehouse management systems go live? Certainly technology has evolved to the point where we can simply press a button and have a WMS in place and be chugging along day one…right?
Let’s look at five ways to basically ensure a botched warehouse management software implementation.
- Be disorganized. On the other hand if you do not want to ensure a botched install, then use a WMS Go Live Checklist or some formal action plan. You can’t just tell your WMS vendor to show up, install, grab “some inventory data”, high-five, and leave. There should be a formal plan for every stage from lead-up to post-implementation support.
- Buy cheap hardware and/or use legacy tech. Do not cut corners on hardware if you are in the market for a smooth implementation, whether getting servers up to the recommended specifications or properly covering the warehouse with Wi-Fi. Underpowering your WMS can at best result in a laggy system, and at worst bring on costly production outages. Error on the side of beefy systems for this expenditure, as hardware only becomes more stressed as the business grows. Also, do not try to force dated or beaten-up tech on the new system. You don’t need to buy the latest and greatest, but toss that scanner gun from the 80s which only works when held at a 32.5-degree angle on Tuesdays. The perceived savings of keeping old hardware is just not worth the risk of bottlenecking and/or introducing compatibility problems.
- Underestimate the importance of good data. If the data isn’t correct, then nothing else will be if you want things to go right. When making cut-over data migration plans from the old system to the new one, at the top of list should be the specific validation that proves that the data was successfully converted/migrated. Not far below that should be the question of how much legacy data to archive in order to prevent, or at the very least limit, slowdowns with the new system. The cross-functional team handling the go live should also have an experienced DBA that is not to be undervalued, and who’s schedule should be focused strictly on the transition. If someone on the team is needed at the drop of a hat, it will most likely be the database specialist.
- Neglect testing. Don’t strictly assume that your WMS is free of defects and that your key process flows are flawless if you want to reduce implementation risk. You should regularly regression and performance test your supply chain systems to identify errors and validate business processes before production is impacted. We have a strong recommendation for a complete, low-code test automation solution that makes creating and maintaining test cases as easy as possible, and with a basic-yet-powerful, streamlined interface and readable test cases we encourage you to reach out to us and see for yourself.
- Skimp on user training and change management. The better trained your users/operators are on day one, the more seamless the implementation. Employees come-and-go these days and training hours aren’t cheap, but your warehouse team (both staff and managers) should be trained on their SOP pre-implementation regardless of how “user friendly” the WMS is purported to be for personnel. This is critical even just from the standpoint of establishing WMS roles and their related restrictions. Many unnecessary problems can be accidentally created by users screwing up a task they were not properly trained to perform.
If you need help preparing for a WMS go live, then feel free to drop us a line! We’ve been helping companies with supply chain execution systems since 2009.
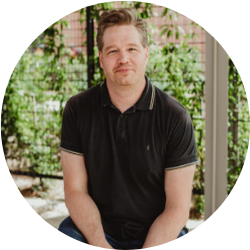
Written By James Prior
With over two decades in software pre-sales and implementation since 2000, James specialized in working with pre-sales teams and contributed to blog posts. For further information, please email sales@tryonsolutions.com.
More From This Category
A Strategic Move: Building your 2025 Budget for a WMS Update
As we approach 2025, it’s clear that staying competitive in supply chain and distribution requires technology upgrades that can improve efficiency, accuracy, and scalability. A key part of that equation is your Warehouse Management System. Whether you’re looking to...
Beat the Competition on Order Fulfillment Accuracy and Speed in 2024
The demands behind customer order fulfillment speed and accuracy ultimately drives nearly everything that happens in a warehouse. Customer expectations continue to increase in 2024, with no signs of abating in the coming years. Streamlining processes and logistical...
The FDA is NOT FUNNY, But this is…
There is not a lot of funny business when it comes to compliance in the warehouse, but to stay on top of the FDA 21 CFR Part 11 mandate, we’ve added a bit of flavor.1. Know the Rules Like a Super FanImagine the regulation is your favorite TV show. Binge-watch,...