TRYON BLOG
How to Use a WMS to Reconcile Inventory

How often does your actual available stock differ from what’s on record? The inevitable wrangling with inventory discrepancies happens even in the most tightly controlled warehouses and distribution centers. Common culprits include putaway bungles and inventory not being synchronized between systems, but we’ll look at all of the usual suspects and then go over how to use a WMS to help handle inventory reconciliation.
Common Causes:
- Receiving and putaway mistakes, which are certainly more likely to happen with poorly trained warehouse staff and/or no WMS in place
- Suppliers sending incorrect shipment data or even worse, the contents of load(s) are solely in printed/handwritten form with the shipment itself
- Labelling that is hard to read/scan or easily rubs off
- Disorganized storage, which is common if you have a lot of inventory with no slotting strategy, a subpar WMS or – egads! – a fully manual system
- Shrinkage due to theft, damage, spoilage, or loss to the deep dark recessed corners of the warehouse
- Inventory being received at the warehouse, but the transaction never makes it to the relevant systems (ERP, WMS, etc…)
- Poorly managed returns
How to Avoid:
- CYCLE COUNTING
You must regularly cycle count, and certain items should be tallied more than others depending on how much they cost, popularity, expiration date, and other factors. Your operation simply can’t afford to lose pricey items in the shuffle often, but relatively cheap ones aren’t worth the labor hours required to meticulously keep track of them. For example…
…Costly items such as mobile phones should be counted frequently
…Ear buds for those phones could be counted less frequently
…Printed pamphlets for the phones could be counted even less frequently
Automatic cycle counts for especially high-dollar items are an option. A WMS can be configured so that an automatic cycle count is triggered right after picking a specific item of inventory, this way you can keep more precise track of products deserving of the extra attention.
- ERP AND WMS
Often times inventory inaccuracies are caused by systems not being fully aligned. Your team must monitor and resolve data transactions (both ways) between the ERP and WMS. If a transaction fails, and no one does anything about it, then our inventory can be thrown off. This is not always limited simply to the item count being wrong, but even an incorrect inventory status can be the culprit. For example…
…In the ERP system a user marks two pallets of an item off “hold” status, but the WMS never receives this change. The problem arises when the ERP sends down an order for the item, but the WMS can’t fulfill the order because it still thinks the item is on hold. Ideally your operation would have regular automatic inventory synchronization between ERP and WMS where all of the WMS inventory counts and their statuses are compared to against the data in the ERP system, and in-turn a report is generated that would reveal any discrepancies and notify the requisite managers.
- WHAT ELSE?
- Suppliers should send shipment data in a common standardized format
- Keep your WMS up-to-date to take advantage of the latest and greatest inventory tracking features
- Focus on loss prevention and security
- Regularly review/consider slotting strategies, standard operating procedures, process improvements, and be sure to conduct related training for warehouse personnel
- Have a world class support team on-call to help with any systems that touch inventory (ERP, WMS, etc…)
- Anywhere automation handles a process or task generally reduces the chance of human error
How to Handle in Your WMS:
If you have identified the root cause and know what needs to be adjusted, then you simply need to alter the quantity of inventory item(s) and can either make an inventory adjustment in your WMS or directly manipulate the data via updating a database table. Regardless of how you make the change be sure to adjust the ERP side accordingly.
If you have not identified the root cause and don’t know which inventory is off or by how much then you should:
- Perform a Cycle Count / Audit. The WMS user will be directed to a location in the warehouse where they scan all of the items found in that location and if the count matches the WMS, then they would fist-pump and move on to the next location. If it doesn’t match, then the user should angrily shake their fist towards the sky, repeat the count (optional depending on WMS configuration) and if the numbers remain off then an inventory adjustment is triggered.
- Get to the bottom of the issue by…
…Checking with warehouse personnel that work in the location(s) involved
…Searching around the location(s) looking for labels that fell off
…Investigating the data flow starting with when it first arrived from the supplier
…Comparing both physical and WMS counts with numbers in any other related systems
…Looking around for a shady warehouse employee slinking towards the exit while nonchalantly whistling with an outline of the missing box poking out from their shirt
A Handy KPI:
Inventory Accuracy Percentage = Physical Count / Record Count X 100
Inventory accuracy percentage can be a helpful benchmark to track if you are regularly dealing with inventory issues, and your operation should shoot for 98 percent or higher.
Are you continually experiencing inventory discrepancies? If you need help, please drop us a line!
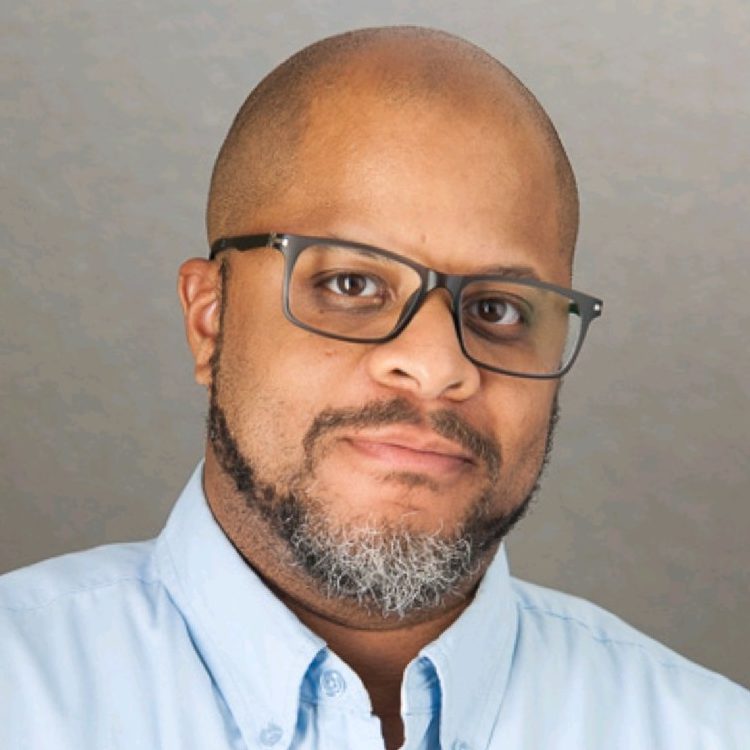
Co-Written By Brian Henry
Brian has been working with supply chain applications, including the Red Praire/JDA/Blue Yonder suite, for 20+ years and has worn multiple hats throughout including Application Support, Development, Business Analyst, and Senior Customer Care Manager. Drop him a line at: brian.henry@tryonsolutions.com
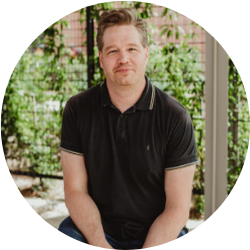
Co-Written By James Prior
With over two decades in software pre-sales and implementation, James specialized in working with the sales team and contributed to blog posts. For further information, please email sales@tryonsolutions.com.
More From This Category
A Strategic Move: Building your 2025 Budget for a WMS Update
As we approach 2025, it’s clear that staying competitive in supply chain and distribution...
Beat the Competition on Order Fulfillment Accuracy and Speed in 2024
The demands behind customer order fulfillment speed and accuracy ultimately drives nearly...
The FDA is NOT FUNNY, But this is…
There is not a lot of funny business when it comes to compliance in the warehouse, but to stay on...