Top Five Latest Warehouse Technologies and WMS Features (Outside of Robotics)
Technology furiously marches on in the warehouse space, and we’ve especially seen marked improvements in hands-free options, smart vehicles, and robotics…but please don’t let the glimmer from the shiny, fancy robot blind you from the slightly-less sexy improvements like hands-free mobile solutions and easier-to-use WMS interfaces. Let’s look outside the realm of AI-driven robots and cobots, as they are hogging the limelight, and look at other technologies that can boost efficiency and productivity in your warehouse or distribution center.
- For your WMS, TMS, and LMS there should be an automated testing solution in place reducing your business risk. Manual testing is pricey and inconsistent in terms of depth and coverage, and we know praying to the warehouse gods (hail carries?) for zero downtime from defects doesn’t work. You need a testing solution for individuals and teams that want to regularly test their supply chain systems and processes to identify errors before production is impacted – and ultimately make implementations and upgrades both smoother and faster. Testing is the single most important facet of software implementation, and it often directly impacts the success or failure of a project. We recommend using a complete, enterprise-worthy low-code test automation for warehouse management and related systems, it MUST make creating and maintaining test cases as easy as possible, and should have a basic-yet-powerful interface and readable test cases so teams can quickly ramp up their automated testing. We can help you select the right one.
- Until we get pick-by-telepathy, pick-by-voice and – more recently – pick-by-vision will have to do. The goal of these hands-free systems is to increase efficiency and accuracy of pickers. In pick-by-voice the operator is given instructions via headset, on what to pick and where, and the operator can give feedback to the system if needed. The voice-picking system will verbally direct the operator to a specific location in the warehouse, and then he/she will verify it was the correct location. The system then verifies that the operator is in the right spot, and gives pick quantity which is confirmed by the operator. Once the pick is completed, the operator is then sent to the next location. The big advantage is not just freeing up hands, but the optimization of the pick path thus maximizing efficiency and minimizing wandering and mis-picks. In pick-by-vision, smart VR goggles collects data internally and externally, and then projects the requisite picking information guiding the operator visually. The goggles can also verify that the correct inventory was picked via built-in bar-code reader. A supplemental bonus to pick-by-vision is it makes the operator look futuristically cool. It’s likely that down the road both voice and vision technologies will be combined to take advantage of the best of both worlds, so stay tuned to pick-by-X technology advancements.
- These days mobile computers/scanners are mandatory for any medium-to-hyuge sized warehouses and distribution centers. They have become integral to the daily SOP in a bustling warehouse or distribution center, as personnel must be able to receive or transmit inventory information anywhere. Imagine receiving inventory at the loading dock without one; typing long inventory numbers instead of quickly and accurately using bar-codes or RFID tags. Mobile technology is always improving, especially in the realms of RFID tags, better ergonomics, hands-free wearability, longer battery life, better durability, and mobile printer attachments. Radio Frequency ID support is one of the more popular overall supply chain tech improvements of the last ten years, as RFID allows tags to not have to be read and this means that the tags themselves can be positioned anywhere since the tag doesn’t have to be visible. These electromagnetic tags can communicate with your WMS and automatically document the comings and goings of their related inventory. RFID tags can also store more data than regular bar-codes. If you have older mobile computers/scanners, at least take a look at the latest features available in the new models, check if your WMS supports them from that side, and consider the ROI of upgrading.
- Most people wouldn’t consider user interfaces as hot tech, but they have been getting much easier-to-use in recent years – and think about how often warehouse personnel touch the WMS front-end. The trend is now presenting information in a more logical, intuitive, and streamlined format, thus reducing the need for costly user training, as well as offering more dashboard options especially in the realm of gamification. The gamified dashboards reveal the fastest and most accurate personnel at warehouse tasks, and this friendly competition can help increase warehouse productivity (and increase employee trash talkin’). Check-in to see if the latest version of your WMS has user interface improvements, and if more than a few complex processes have been streamlined into something easier for your warehouse staff then it’s time to do some ROI calculations.
- Autonomous vehicles (or autonomous guided vehicles) can up your storage and retrieval game for clamp-trucks, forklifts, carts, and/or whatever other vehicles you need chugging around your warehouse or distribution center. Driver-assisted options have been around for a while, but the newer self-guided AVs use camera sensors or lasers to navigate through digital paths in the warehouse rather than having to be controlled by warehouse personnel. They can also work individually by collecting and analyzing data on their own, and then responding on-the-fly to obstructions and bottlenecks while acting in concert with other AVs which is known as machine-to-machine “platooning”. Autonomous vehicles are a pricey upgrade, but they can pay for themselves by reducing worker travel, wait times, and overall space optimization – and you don’t need to change the basic layout of your warehouse since they match the footprint of their standard vehicle counterparts. By the way, the difference between autonomous vehicles and drones (aside from land versus air) is that the latter is mainly used for data collection. Newer drones could technically be used to move very small inventory, but their primary function is tracking/counting the inventory whereas AVs transport it. Drones could easily be worth the expense right now if you have a lot of inventory stored on tall, many leveled shelving racks. And no, the movie Maximum Overdrive isn’t going to happen in your warehouse.
What new tech are you seeing out there in the warehousing and logistics world? Drop us a line and let us know!
This post was written by:
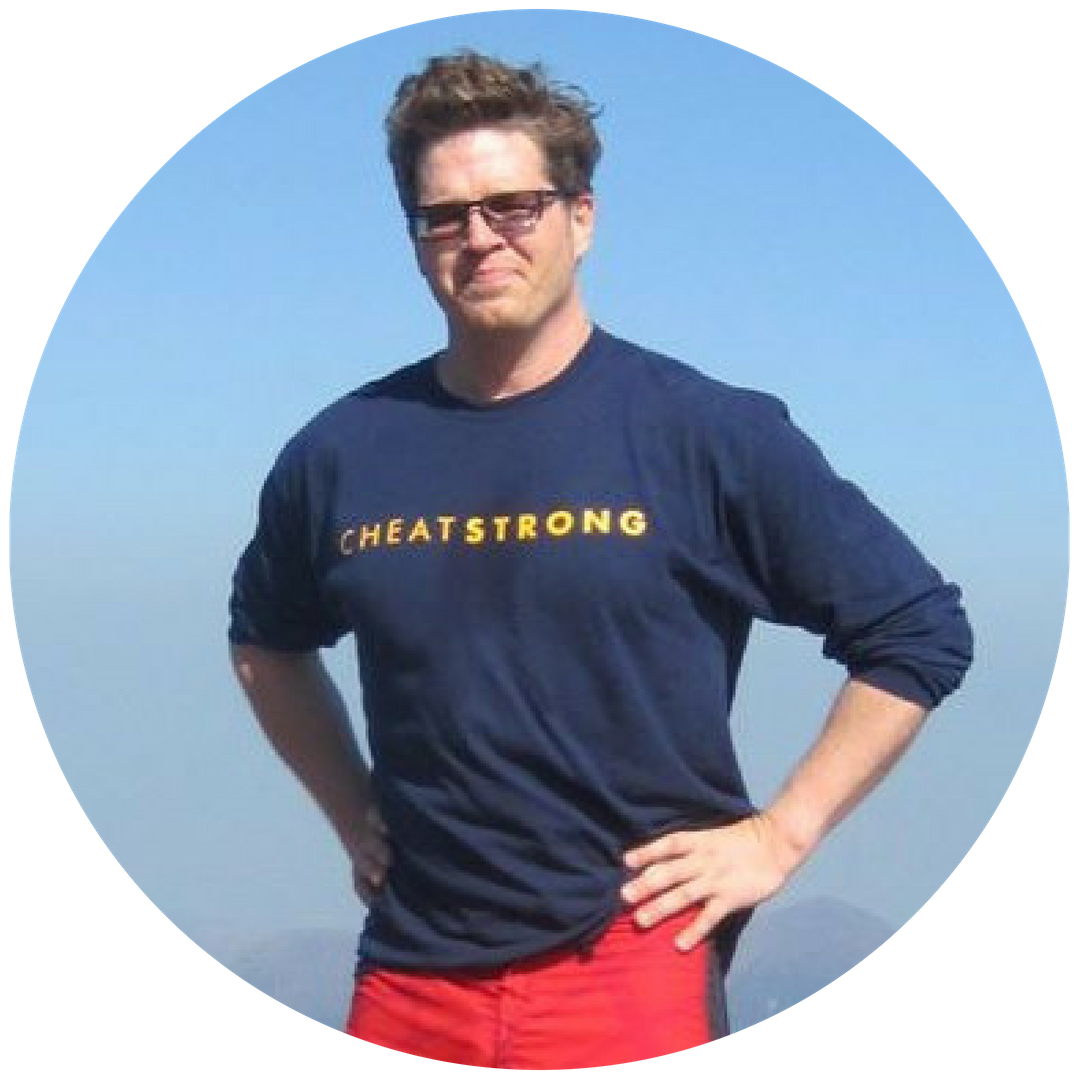
James Prior
Sales Ops Manager
James has been working in software pre-sales and implementation since 2000, and more recently settled into working with a pre-sales team and occasionally writing blog posts. Drop him a line at: james.prior[at]tryonsolutions[dot]com.
Recommended Content
A Guided Tour of Supply Chain Execution Systems
Supply Chain Execution (SCE) systems are behind the process workflows of goods going from procurement to delivery in the supply chain. SCE comes after Supply Chain Planning (SCP), and both are under the umbrella of Supply Chain Management (SCM) systems. In this...
WMS Go Live Checklist Download
Keep in mind that this checklist is a starting point. Adapt it to fit your WMS project's specific needs. Understand your project's unique requirements and customize the checklist accordingly.
Performance Testing Your Warehouse Management System
We’ve made the case for automated testing in various blog articles with a regression testing focus, but we can’t neglect the importance of performance testing. It’s critical for warehouses to determine for their supply chain systems an answer to the question: At what...
Top 5 Ways You Could Botch Your Next WMS Go Live
Are things running too smooth? Have you had it too easy in the supply chain world these days, and want to challenge yourself by botching a warehouse management systems go live? Certainly technology has evolved to the point where we can simply press a button and have...
13 Burning Questions for a Pioneer in Warehouse Modernization
Trevor Blumenau is a professional engineer with a master’s degree in robotics from UC Berkeley and has 25 years of R&D experience in warehouse/manufacturing processes, controls, and innovation. Trevor founded Voodoo Robotics to modernize warehouse operations by...